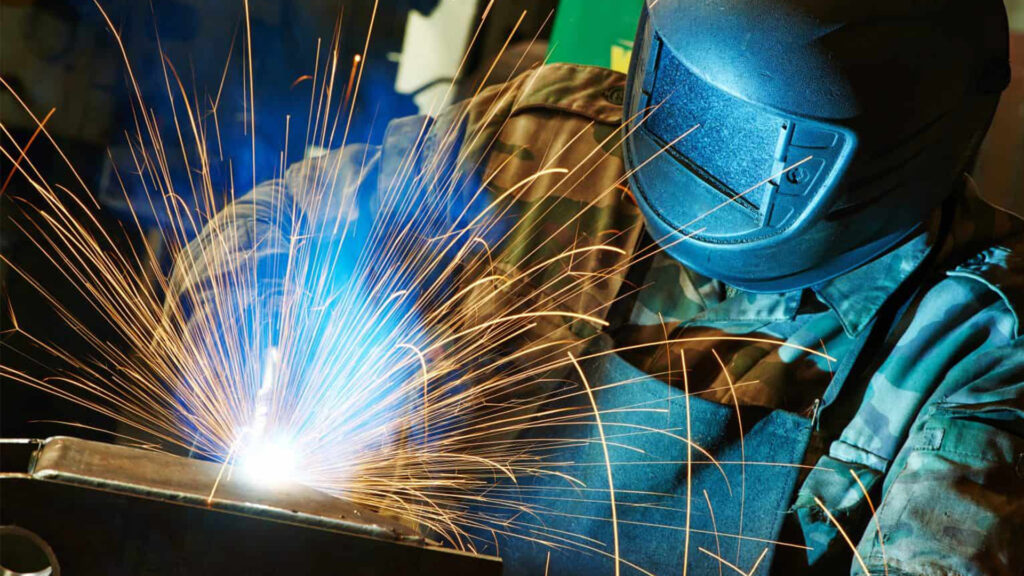
Common Problems with Leather Welding Jackets: What You Need to Know
Introduction
Leather welding jackets are a staple in the protective gear of welders worldwide. Known for their durability and resistance to heat and sparks, these jackets are essential for safety. However, like all products, leather welding jackets come with their own set of challenges that can affect their performance and user satisfaction. In this article, we explore the common problems associated with leather welding jackets and provide insights into what every welder needs to know to make informed choices.
1. Weight and Comfort Issues
One of the primary complaints about leather welding jackets is their weight. Leather, being a natural material, tends to be heavier than synthetic alternatives. This can lead to fatigue and discomfort, especially during long welding sessions. The added weight can also restrict a welder’s mobility, making it difficult to perform tasks that require flexibility.
2. Heat Retention
While leather’s heat resistance is a key benefit, it can also be a drawback. Leather jackets tend to retain heat, which can become uncomfortable in already hot working environments. This can lead to excessive sweating, dehydration, and heat exhaustion if not properly managed.
3. Limited Breathability
Another significant issue with leather welding jackets is their lack of breathability. As they are designed to protect against sparks and heat, these jackets often sacrifice ventilation, which can cause the wearer to overheat and experience discomfort.
4. Maintenance and Durability
Leather requires more maintenance than fabrics like cotton or synthetic blends. It needs to be regularly treated with leather conditioners to prevent it from drying out and cracking. Additionally, inconsistent leather quality can affect the jacket’s durability, leading to early wear in areas exposed to frequent movement or heat.
5. High Cost
The cost of high-quality leather welding jackets can be a barrier for many. Leather is more expensive to produce and treat than many other materials, which is reflected in the retail price. This can be a significant consideration for welders or employers purchasing gear in bulk.
6. Flexibility and Fit
Leather jackets can be quite stiff, especially when new. This stiffness can hinder a welder’s ability to move freely, which is crucial in avoiding workplace accidents. Moreover, finding the right fit can be challenging, as leather does not stretch to accommodate different body shapes as some other materials do.
7. Environmental and Health Concerns
The production of leather often involves chemicals that can be harmful to the environment. Additionally, some welders may experience allergies or sensitivities to the dyes and treatments used in leather products, leading to skin irritation or other health issues.
8. Chemical and Water Resistance
Leather is not inherently resistant to chemicals and water, which can be a significant drawback in environments where exposure to such elements is common. Water can cause leather to become heavy and stiff, while chemicals may degrade the material more quickly than expected.
9. Style Limitations
While functionality is paramount in safety gear, aesthetics also play a role in user satisfaction. Leather welding jackets often come in limited styles and colors, which may not appeal to all users.
10. Special Care Requirements
Unlike fabric jackets, leather requires special care. It cannot be washed in a conventional washing machine and needs specific cleaning techniques, which can be cumbersome for users who do not have the time or resources to maintain their jackets properly.
Conclusion
Despite these issues, leather welding jackets remain a popular choice due to their protective qualities. However, understanding these common problems can help welders and employers make more informed decisions about their protective gear. By considering alternatives, exploring new materials, or investing in higher-quality leather, it is possible to mitigate some of these challenges. Remember, the right protective gear is crucial not only for safety but also for ensuring comfort and productivity on the job.
Final Note
For those in the market for a new welding jacket, weigh the pros and cons of leather against your specific needs and environment. Innovations in materials technology may offer new solutions that address these traditional pain points without sacrificing protection.