Do Leather Welding Jackets Truly Deliver the Quality and Durability You Deserve?
Do Leather Welding Jackets Truly Deliver the Quality and Durability You Deserve?
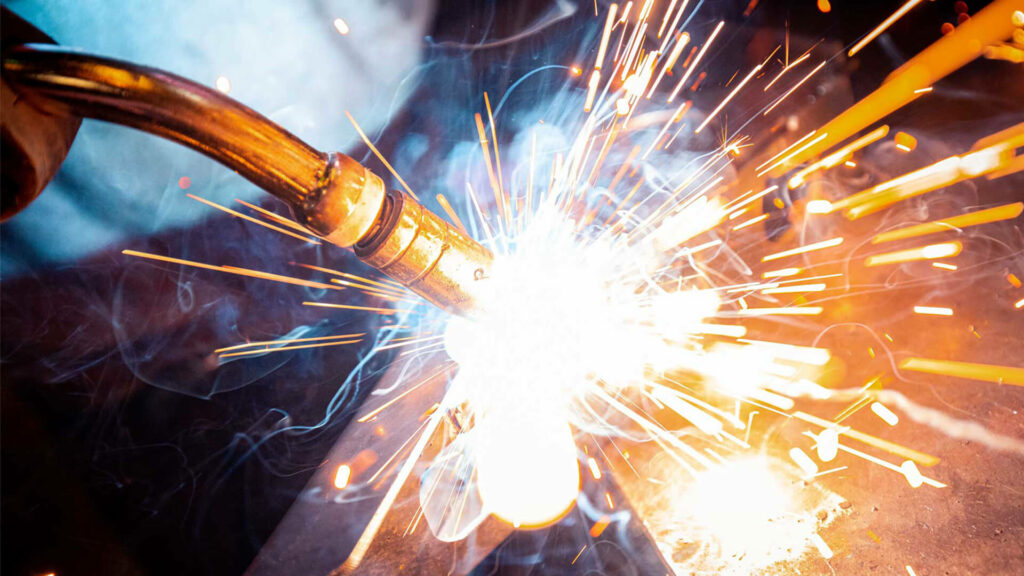
Are you tired of constantly replacing your protective gear, only to find that your leather welding jackets still don’t stand up to the rigors of your daily work? In the challenging world of welding, safety is paramount, and leather welding jackets are often considered a crucial line of defense. However, many users and buyers alike question whether these jackets truly offer the quality and durability they promise. From the type of leather used to the construction methods employed, there are a host of shortcomings that can undermine the very safety they are intended to provide. In this comprehensive guide, we’ll explore the key issues affecting leather welding jackets and help you decide how to safeguard your welding operations more effectively.
Are Leather Welding Jackets Truly Indispensable for Welding Safety?
Before diving into their shortcomings, you might ask: Are leather welding jackets really so essential? When exposed to molten metal, flying sparks, and extreme heat, welders need reliable protective clothing that can withstand heavy-duty conditions. Leather has long been a favorite for welding jackets due to its heat resistance, durability, and capacity to shield users from burns and abrasions.
Yet, is the leather you’re purchasing for your team up to the task? High-quality leather can indeed offer excellent insulation against sparks and moderate flame. However, not all jackets are created equal. If the leather is low-grade, if the stitching is weak, or if the lining is inadequate, then even the most expensive jacket won’t stand the test of time—or the test of safety.
What Are the Most Common Quality Pitfalls in Leather Welding Jackets?
1. Could Inferior Leather Be Compromising Your Safety?
Have you ever wondered why some leather welding jackets feel softer or thinner than others? The answer often lies in the grade of the leather itself. High-grade leather—such as full-grain or top-grain—offers superior resistance to heat, sparks, and wear. In contrast, lower-grade or synthetic leather frequently cracks, peels, or degrades under welding conditions.
- Why it matters: If the leather is subpar, it may not shield you properly from burns, leading to injuries and potential downtime.
- What to look for: Full-grain leather is generally considered the gold standard, but it comes at a higher cost. Checking product specifications or certifications can help you verify the quality.
2. Is Poor Stitching Putting You at Risk?
Can a single thread really compromise an entire jacket? Unfortunately, yes. Stitching integrity is critical to safety gear, especially at stress points like the shoulders and sleeves. When stitching fails, tears and holes can form, exposing welders to sparks and heat.
- Why it matters: Weak or poorly done seams can come undone, reducing the life of your jacket and putting your team at risk.
- What to look for: Double-stitched seams with flame-resistant thread provide additional strength. Reinforced areas—like elbows and underarms—are also a must.
3. How Does Inadequate Reinforcement Shorten Jacket Lifespan?
Do you notice worn-out elbows or frayed edges on your current welding jackets? High-friction areas demand extra reinforcement to prevent early wear and tear. Without it, the jacket may deteriorate quickly in the exact spots where you need the most protection.
- Why it matters: A jacket that wears out prematurely wastes your budget and leaves welders with insufficient coverage.
- What to look for: Reinforced panels or patches in high-wear zones such as elbows, shoulders, and seams can significantly extend a jacket’s lifespan.
4. Could a Substandard Protective Lining Be a Hidden Danger?
Have you ever felt that a welding jacket just doesn’t provide enough insulation? The inner lining is key to keeping welders comfortable and safe from intense heat. When the lining is thin or made of low-quality materials, it can fail to block heat effectively, leading to burns and an uncomfortable working environment.
- Why it matters: Poor insulation increases the risk of burns, even if the outer leather seems sufficient.
- What to look for: Look for multiple layers of flame-resistant linings, often labeled as FR-rated or tested according to international standards.
Why Do So Many Leather Welding Jackets Fall Short on Durability?
1. Will Continuous Use Wear Them Down Faster Than You Expect?
Is your welding team doing repetitive tasks for hours on end? Continuous exposure to sparks, slag, and heat can degrade leather over time. The question is, how fast should a jacket realistically wear down? A truly durable jacket should last through months—or even years—of constant use, depending on the intensity of the workload.
- Why it matters: Early wear and tear can drain your budget with frequent replacements.
- What to look for: Jackets designed for heavy-duty tasks that emphasize thick leather and robust construction can better withstand daily use.
2. Can Harsh Environments Accelerate Deterioration?
Do you work in environments with not just heat and sparks, but also chemical exposure? Leather jackets not treated for chemical resistance may degrade or fade quickly, reducing their protective capabilities.
- Why it matters: Prolonged contact with chemicals or corrosive substances can weaken the jacket’s fibers and compromise safety.
- What to look for: If chemical exposure is a concern, opt for leather jackets specifically treated to resist chemicals, or consider using an additional protective layer.
3. Is Lack of Comfort Also a Durability Issue?
Does it seem odd to lump comfort in with durability? Actually, uncomfortable jackets often lead to improper usage. When workers are restricted by stiff materials or poor fit, they may take shortcuts or avoid wearing protective gear altogether.
- Why it matters: A jacket left hanging on a rack offers zero protection. If a welder won’t wear it, the jacket—no matter how durable it is—becomes irrelevant.
- What to look for: Seek ergonomic designs, articulated sleeves, adjustable cuffs, and breathable linings that encourage welders to keep their safety gear on.
4. Will Color Fading and Material Degradation Influence Performance?
Have you noticed jackets turning a dull shade after just a few weeks or months? Prolonged exposure to high heat and bright light can cause leather to fade. Although color fading itself might be cosmetic, it can signal deeper material degradation.
- Why it matters: Degraded leather can crack and weaken, reducing its ability to protect against sparks and flames.
- What to look for: Some manufacturers apply UV-resistant treatments or specialized dyes that help the jacket retain its color and integrity longer.
How Can You Spot a High-Quality, Durable Leather Welding Jacket?
Are you ready to make a more informed decision next time you purchase leather welding jackets? Consider these key checkpoints:
- Grade of Leather: Insist on full-grain or top-grain leather, which generally provides better heat resistance and longevity.
- Stitching Quality: Look for double-stitched seams with flame-resistant thread, especially around stress points like elbows and shoulders.
- Reinforcement: Check for additional patches or layers in high-wear zones.
- Protective Lining: Ensure there’s a robust flame-resistant liner that can withstand heat and sparks.
- Brand Reputation: Opt for brands known for stringent quality controls and positive user feedback.
Is the Future of Leather Welding Jackets Changing for the Better?
Wondering if manufacturers will address these quality and durability challenges in the coming years? With rising competition and evolving safety standards, many brands are already investing in research and development to enhance materials, construction methods, and comfort features. Here’s what you might see soon:
- Advanced Material Treatments: Innovative coating or tanning processes that boost heat and chemical resistance.
- Smart Technology Integration: Sensors embedded in jackets to monitor temperature and potential fabric damage in real time.
- Sustainable Leather Sourcing: More eco-friendly practices and certifications that help reduce environmental impact without compromising on protection.
- Modular Designs: Interchangeable components for easier repairs, upgrades, and extended lifespan.
Will You Demand More from Your Leather Welding Jackets?
So, are leather welding jackets delivering the quality and durability you truly deserve? In many cases, the answer is a resounding “not yet.” From inferior leather to poor construction, the market is brimming with jackets that fail to live up to their promise. Yet, awareness is the first step toward better protection. By focusing on high-grade materials, reinforced construction, and robust design features, you can elevate your welding safety program and save money in the long run.
Ready to upgrade your leather welding jackets and improve overall welding safety? Whether you’re a buyer exploring bulk orders for a manufacturing facility or a welder looking to invest in personal protective equipment, remember that durability and quality are non-negotiable. After all, it’s not just about protecting your bottom line; it’s about protecting the people who are essential to your operation. Demand more from your gear, and watch as reliability, safety, and peace of mind become the new norm in your welding environment.