Behind the Scenes of China’s Top 10 Welding Safety Manufacturers: Price, Process, and Innovation
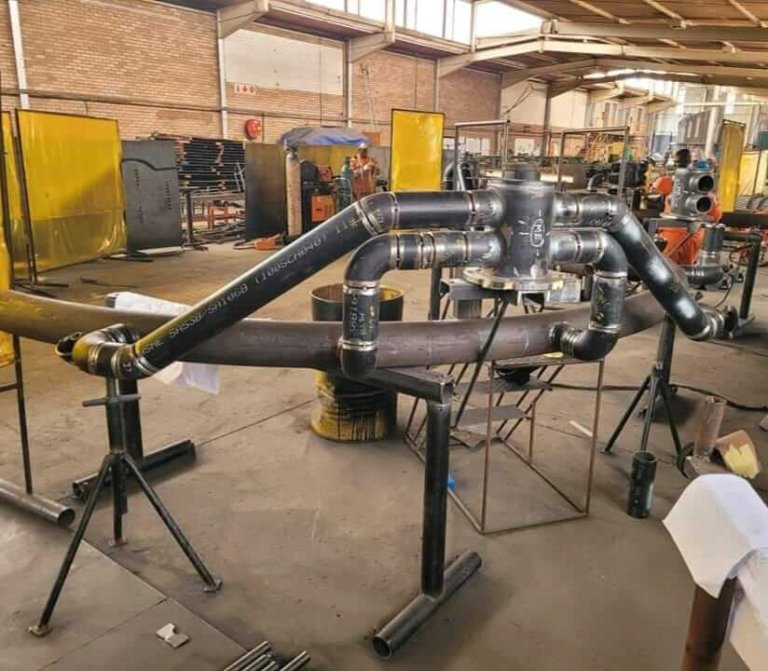
Welding is a cornerstone process in industries that range from heavy construction to intricate metal arts. It involves the fusion of metals (or thermoplastics) using high heat to melt parts together, and then allowing them to cool, causing fusion. While the resultant structures are robust and integral to manufacturing across the globe, the very process of welding is rife with potential hazards. Consequently, welding safety is not just a recommendation; it is a critical necessity that must be upheld to protect welders, their colleagues, and the integrity of the final product.
One of the primary reasons welding safety is so vital stems from the multiple risks associated with hot work. The arc produces intense ultraviolet and infrared radiation, which can damage unprotected eyes and skin. Spatter, sparks, and molten metal droplets can cause burns or even start fires in the surrounding environment. Toxic fumes and gases released during welding pose respiratory risks. Thus, personal protective equipment (PPE) plays an indispensable role in mitigating these hazards. Within the realm of PPE, there are several key items specifically designed for welders: welding blanket, welding jacket, and welding apron. Each serves a distinct function, providing layers of protection for the welder and the immediate workspace.
Historically, welders often relied on heavy leather jackets and gloves, but over time, technology has given rise to new, flame-resistant fabrics, more ergonomic designs, and specialized accessories. For instance, the concept of the welding blanket—a fire-resistant cover used to shield equipment, floors, or the welder—has evolved significantly. These blankets are now manufactured in multiple thicknesses and materials to address varying temperature requirements and project scopes. Similarly, welding jackets and aprons have come a long way from their early, bulky origins. Today, they are crafted with advanced fabrics that provide superior thermal insulation, spark resistance, and even chemical resistance in certain high-risk environments.
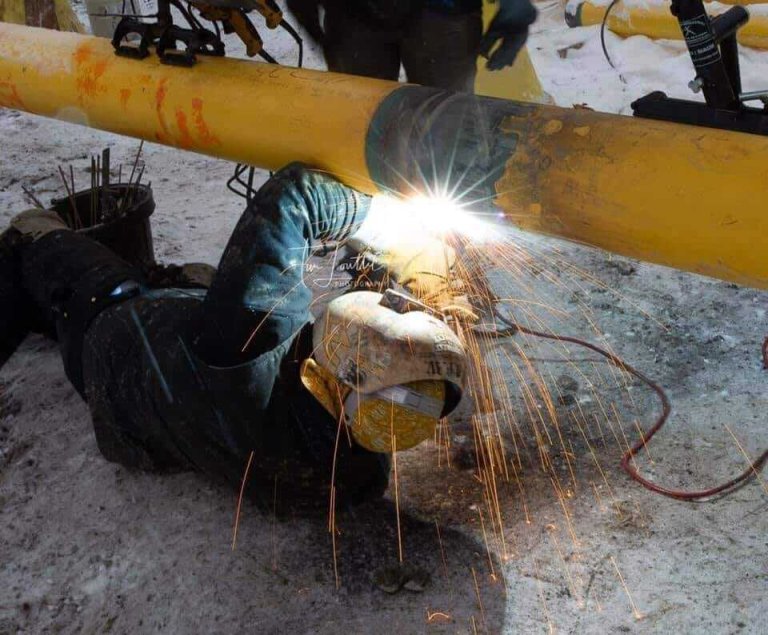
For international buyers, particularly those looking to import from China, a key consideration is identifying a company or supplier that can consistently deliver high-quality, reliable products at competitive price points. China’s industrial evolution has positioned it as one of the world’s top manufacturers of welding safety gear. Not only is there a broad variety of products to choose from, but there are also many specialized custom services available to ensure that items like welding blankets, jackets, and aprons meet specific requirements in terms of dimensions, materials, and branding. Industry players such as Mingshun have responded to growing demand by offering flexible production lines capable of handling both standard and bespoke orders.
The global market for welding safety apparel and accessories is on the rise, with user expectations continuously broadening. On-the-job safety requirements are more stringent than ever, and advanced manufacturing processes enable the creation of protective gear that is simultaneously robust, lightweight, and comfortable. Furthermore, the advent of e-commerce platforms has simplified international transactions, facilitating easier access to top-tier manufacturers. Buyers can now evaluate multiple suppliers, read reviews, verify certifications, and even request samples before committing to large-scale orders.
However, with choice comes complexity. Selecting the right supplier or manufacturer can be daunting, especially when concerns about cost and quality must be weighed against factors like lead times, shipping logistics, and after-sales support. Hence, this guide is dedicated to unraveling the essentials of welding safety products—from understanding what a welding blanket is, to discovering the Top welding safety manufacturer in China, to exploring how best to collaborate with a reputable factory for custom services. We will also delve into the manufacturing process itself, offering insights into how these products evolve from raw materials to finished goods. Throughout, we’ll keep the buyer’s perspective at the forefront, addressing questions about certifications, compliance with international standards, and practical tips for navigating the procurement cycle.
By the end of this detailed exploration, readers should possess not only a firm grasp of the different protective products available but also the knowledge required to make informed decisions. Whether you are a procurement professional seeking the best company for custom solutions, a welding business owner curious about the latest trends, or a safety manager tasked with upgrading protective gear, this comprehensive guide has you covered. Let us begin by investigating the foundational piece of many welding setups: the welding blanket.
Welding Blanket: Applications, and Key Benefits
A welding blanket is one of the most versatile pieces of safety equipment in hot work environments. Its primary role is to protect surfaces, tools, and personnel from heat, sparks, and molten metal that inevitably arise during the welding process. However, calling it a mere “protective covering” undersells its importance. Welding blankets can be the difference between a safe, efficient workspace and one riddled with accidental fires, equipment damage, or severe worker injuries.
What is a Welding Blanket?
At its core, a welding blanket is a fire-resistant fabric designed to withstand high temperatures. It is typically placed over objects or surfaces that might otherwise be vulnerable to sparks or direct contact with welding spatter. Made from materials like fiberglass, silica, or carbon fiber, these blankets are engineered to repel or contain heat. They come in varying thicknesses to cater to different ranges of heat resistance. For example, a standard fiberglass welding blanket might be rated to withstand continuous exposure to temperatures of around 1,000°F (537°C), whereas more specialized silica blankets can handle temperatures up to 1,800°F (982°C) or more.
Industrial and Commercial Applications
Welding blankets are not limited to just welding tasks. They are commonly used in:
- Cutting and Grinding Operations: Sparks from angle grinders or cutting torches can ignite nearby flammable materials. A blanket draped around the workspace forms a protective barrier.
- Maintenance and Repair in Factories: When machinery or pipelines require onsite welding or cutting, a welding blanket provides a quick way to shield adjacent equipment and structures.
- Automotive Repair Shops: Mechanics use them during bodywork, especially when welding or cutting near sensitive parts.
- Oil and Gas Infrastructure: On rigs or pipelines, the risk of fire is extremely high. Welding blankets become a must-have to shield cables, hoses, or flammable surfaces.
- Construction Sites: Structural steel welding often takes place in open areas where wind can blow sparks. Blankets placed strategically prevent accidental fires.
Moreover, for companies or suppliers in China looking to meet the international market’s needs, a diverse product range of welding blankets with different temperature ratings is essential. Such variety ensures that clients across multiple industries can find exactly what fits their requirements. Mingshun, for example, has introduced multi-layer blankets specifically engineered for unique environments, showcasing how a custom, well-designed blanket can vastly improve workplace safety.
Maintenance, Storage, and Lifespan
Maintaining a welding blanket is relatively straightforward but crucial for prolonging its lifespan. After each use, the blanket should be shaken or brushed to remove trapped debris. If it’s coated with a substance, care must be taken to avoid abrasions or punctures. In some environments, the blanket may need to be wiped down with mild cleaning solutions to remove contaminants like oil or chemicals that might compromise its fire-resistant properties.
Storage is another key factor. Welding blankets should be stored in a clean, dry area away from direct sunlight or moisture. Prolonged exposure to UV rays can degrade certain fibers, while excess moisture can lead to mildew or mold in the fabric, especially if the blanket remains folded for extended periods without ventilation. Rolling the blanket rather than folding it is often recommended, particularly for fiberglass or silicone-coated blankets, to prevent creasing.
As for lifespan, a high-quality welding blanket can endure years of intermittent use if properly maintained. However, in high-intensity industrial settings, blankets might need frequent replacement due to wear and tear. Careful inspection before each use—checking for cuts, burns, or broken fibers—is key to ensuring continued protection. Once a blanket shows serious signs of damage, it should be replaced rather than repaired, as even minor tears can compromise its integrity in high-heat scenarios.
Key Benefits
- Thermal Protection: The primary advantage is obvious—protecting personnel and equipment from hazardous temperatures.
- Fire Prevention: By containing sparks and spatter, a welding blanket substantially reduces the likelihood of accidental fires.
- Versatility: Blankets can be used in welding, cutting, grinding, or any other hot work environment.
- Reusability: With proper care, a welding blanket can be used multiple times, making it a cost-effective safety solution.
- Custom Options: Many manufacturers, including Mingshun, offer custom sizes, shapes, and material compositions to suit specialized applications.
Ultimately, whether you are a hobbyist welder or managing a large production plant, investing in quality welding blankets is an essential step in fortifying overall safety protocols. With varied materials, temperature ratings, and coatings available, buyers should tailor their choice to the specific demands of their operation. In the following sections, we will explore other critical PPE items—welding jackets and welding aprons—that complement the protective role played by welding blankets, forming a complete safety suite for modern welding environments.
Choosing the Right Fit for Different Tasks
Selecting between a welding jacket and an apron involves multiple considerations:
- Nature of the Welding Task: Overhead welding or high-intensity processes (like flux-cored arc welding or plasma cutting) typically necessitate a jacket for better coverage. Lower-intensity tasks or those requiring frequent arm mobility might be well-served by an apron.
- Work Environment: In enclosed spaces with limited ventilation, wearing a heavy jacket can be uncomfortable. An apron with partial sleeve coverage may strike the right balance.
- Climate and Temperature: Hot, humid climates can make thick leather jackets unbearable. Flame-resistant fabric jackets or aprons might be a better option in such conditions.
- Frequency of Use: Professional welders who spend hours daily near an arc need high-quality, durable materials that can withstand frequent wear and tear. Hobbyists might manage with more budget-friendly, standard options.
Companies in China that specialize in welding safety gear often offer a comprehensive catalog of both jackets and aprons. By partnering with a reputable supplier or factory, buyers can even request custom modifications. These might include adjustable straps, personalized color schemes, or integrated branding that aligns with corporate requirements. For instance, Mingshun provides tailor-made solutions where clients can specify materials, sizes, and design elements that cater to unique operational needs, ensuring that everyone from small workshops to large-scale manufacturing facilities can obtain exactly what they require.
Furthermore, the price and cost of a welding jacket or apron can vary significantly based on the materials used, additional protective features, and the complexity of the manufacturing process. Leather garments generally fetch higher prices due to their robust nature and longer production times. High-tech flame-resistant fabrics might also command a premium, especially if they contain proprietary blends or advanced coatings. However, with economies of scale and strong competition in the Chinese market, buyers can still secure competitive quotes—even for high-quality, custom products.
Top Welding Safety Manufacturer in China: Key Players and Market Trends
China has cemented its position as a global industrial powerhouse, and in the realm of welding safety equipment, it hosts numerous top-tier manufacturers. These companies produce a wide range of products—from the welding blanket and welding jacket to the welding apron—and ship them worldwide. In this section, we’ll look at the Top welding safety manufacturer in China, discuss the criteria that put them on the list, and explore emerging market trends shaping the country’s welding safety sector.
The Rise of China as a Global Supplier
Over the past few decades, the Chinese manufacturing sector has evolved from a low-cost labor hub to a sophisticated network of factories and research centers capable of producing technologically advanced solutions. Innovations in automation, coupled with massive domestic demand, have fostered a competitive environment among companies, driving them to improve product quality, reduce cost, and implement stringent quality control systems.
Today, Chinese factories that specialize in welding safety gear often house modern equipment, such as automated cutting and stitching machines, advanced quality testing facilities, and research laboratories for developing new flame-resistant materials. This shift in capabilities has not only lowered the production price for many items but also maintained or improved product reliability—two factors that appeal strongly to global buyers.
Criteria for Selecting Top Manufacturers
Several parameters help identify leading Chinese welding safety manufacturers:
- Quality and Compliance: Adherence to international standards like ISO 9001 for quality management, and certifications relevant to flame-resistance (e.g., NFPA 2112, EN ISO 11611).
- Product Range: The ability to supply multiple types of welding safety gear—blankets, jackets, aprons, gloves, and more—often indicates a well-rounded production capability and resource pool.
- Export Experience: Companies with a proven track record of shipping globally understand the complexities of international logistics, customs, and regulations.
- Customer Support: After-sales services, responsiveness, and willingness to offer custom
- Innovation and R&D: Continuous investment in research and development to improve materials, designs, and manufacturing processes.
Emerging Market Trends and Innovations
China’s welding safety market is experiencing dynamic shifts propelled by a combination of technological advancement and increased global safety awareness. Key trends include:
- Eco-Friendly Materials: Manufacturers are exploring biodegradable or low-impact flame retardants to reduce the environmental footprint of production.
- Smart Clothing: R&D teams are experimenting with sensors integrated into jackets to monitor ambient temperature, user posture, or even detect harmful gases.
- High-Performance Coatings: New coatings can deflect not just heat, but also airborne contaminants, boosting the functional lifespan of protective gear.
- Shorter Lead Times: Fierce competition drives companies to streamline production and shipping, decreasing the waiting period for international customers.
Buyers should pay special attention to whether these manufacturers offer OEM or ODM capabilities, as these services allow for greater brand customization. Many Chinese companies are open to producing private-label items, letting importers from around the globe resell the gear under their own brand names. While price and cost are major considerations, intangible factors—like the level of service offered, responsiveness to inquiries, and post-purchase support—play a substantial role in building a sustainable partnership.
All in all, the welding safety product landscape in China is rich with opportunity. From established giants like Mingshun to rising stars like FireTek Solutions, each company brings unique strengths to the table. By understanding the nuances of each manufacturer’s offerings and aligning them with project requirements, international buyers can secure high-quality, competitively priced welding safety gear. The next step involves evaluating potential company or supplier partnerships in greater detail, ensuring that you identify the perfect fit for your specific needs. Let us now shift focus to practical guidelines for selecting the right welding safety provider and forging a lasting, mutually beneficial relationship.
Selecting the Right Welding Safety Company and Supplier
Choosing the ideal company or supplier in the welding safety sector—whether for a welding blanket, welding jacket, or welding apron—can profoundly influence project outcomes. A reliable partnership can help you secure top-quality products, navigate logistical hurdles, and sustain a consistent supply chain. Conversely, partnering with a disorganized or subpar supplier can result in delays, cost overruns, and quality compromises. This section outlines key steps and best practices to guide your supplier selection journey, particularly when sourcing from China.
Questions to Ask Prospective Suppliers
Conducting a thorough vetting process is fundamental. Here are key questions that can illuminate a supplier’s capability and reliability:
What Certifications Do You Have?
Look for quality management certifications like ISO 9001, alongside product-specific approvals such as CE, NFPA 2112, or EN ISO 11611. This ensures their welding safety gear meets recognized international standards.
What Is Your Production Capacity?
If you plan to place sizable orders or require fast turnaround, confirm that the supplier’s factory can handle your volume. Smaller factories might excel at customization but struggle with large-scale orders.
Do You Offer Custom Services?
For specialized needs, including branded gear or unique material specifications, a supplier that embraces custom production is invaluable. Inquire about minimum order quantities (MOQs) and lead times.
Can You Provide Product Samples?
Sampling allows you to evaluate product quality firsthand. Be prepared to pay for both the sample and shipping, but consider it an investment in risk mitigation.
How Do You Handle Quality Control?
Ask about their testing protocols for heat resistance, flame retardancy, stitching durability, and other relevant attributes. Quality audits and inspections should be routine, not ad hoc.
Do You Have Export Experience?
Suppliers with established export processes are likely familiar with global logistics, customs documentation, and shipping regulations, making it smoother for you to import goods.
What Is Your After-Sales Service Policy?
Understand the supplier’s policy on returns, refunds, or replacements. A strong after-sales program indicates confidence in their product quality and a commitment to customer satisfaction.
Supplier Verification and Audits
Even if a supplier seems promising on paper, on-site audits or third-party verifications can provide peace of mind. Larger buyers often hire local agents or inspection companies to evaluate a factory’s production lines, storage facilities, and administrative systems. Key elements typically reviewed during these audits include:
- Manufacturing Equipment: Are they up-to-date and well-maintained?
- Workforce Skill Level: Do operators have the necessary training and experience?
- Safety and Compliance: Does the factory follow mandated labor and safety regulations?
- Material Storage Conditions: Are raw materials properly labeled and stored to avoid contamination?
- Production Flow and Efficiency: Is the factory capable of meeting tight deadlines?
While an in-person audit might be challenging due to geographic distance or travel restrictions, virtual audits—where suppliers offer live video tours—are increasingly popular. Another option is to consult references from existing clients, asking about their experiences with quality control, timeliness, and overall communication.
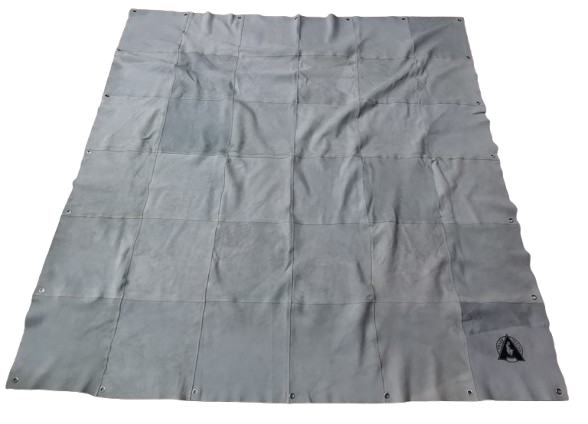
Sourcing a welding blanket, welding jacket, or welding apron can be a complex undertaking, especially when factoring in process details, custom options, price considerations, and the need for consistent quality. Yet, armed with a comprehensive understanding of the market, the manufacturing life cycle, and the best practices for selecting and collaborating with top-tier manufacturers in China, buyers can confidently navigate this landscape. Remember that each step—from vetting the factory to negotiating costs and verifying certifications—plays a critical role in ensuring you receive products that offer outstanding protection and value. Whether you partner with industry leaders like Mingshun or explore other reputable names, prioritizing quality, safety, and transparent communication will lay the foundation for a successful, long-term procurement strategy.
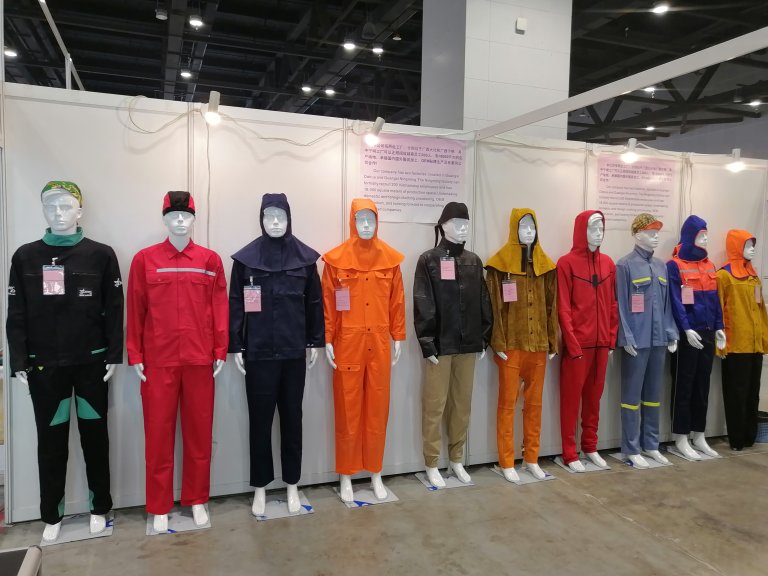