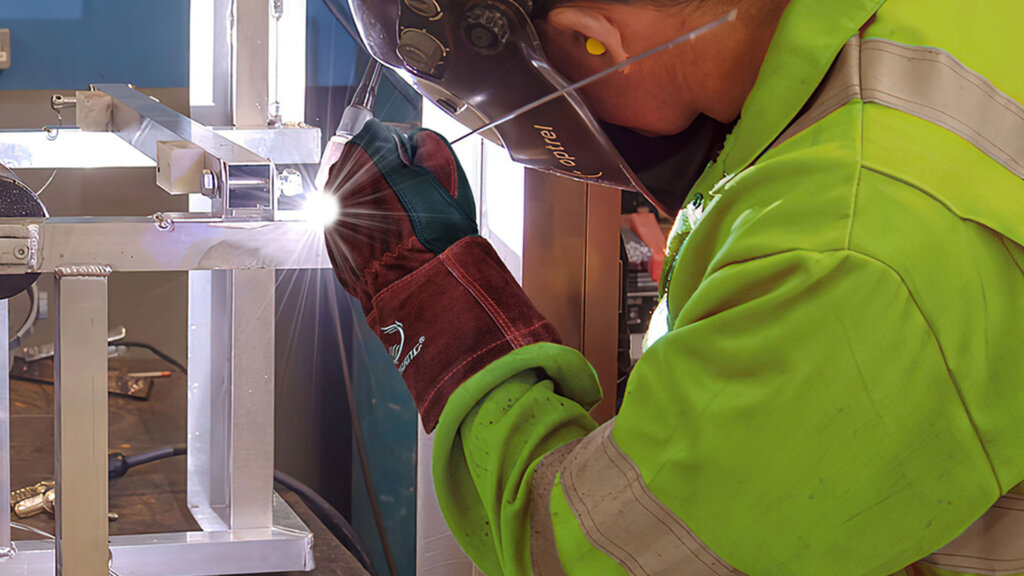
Is Your Leather Welding Jacket a Hidden Nightmare? Discover How to Avoid Costly Mistakes and Find the Best Protection
Are you a welding professional who relies on leather welding jackets for daily protection? Do you worry that subpar or deceptive leather quality could compromise your safety, comfort, and overall investment? Have you ever wondered why some so-called “famous” brands fail to meet your expectations—even when they promise the moon? Could it be that you are paying more for a label than for real protection?
In a world overflowing with marketing claims and brand reputations, how can you make a truly informed choice about your next welding jacket? Shouldn’t you explore the hidden pitfalls—the “nightmares”—that can arise from poorly sourced or improperly treated leather? With so many brands trying to grab your attention, isn’t it worth taking a deeper look at why certain leather welding jackets promise much but deliver little?
If you find yourself asking these questions, you’re not alone. Many buyers worry about wasting money on jackets that wear out prematurely, inhibit their movement, or reek of strong chemical odors. Do you want to avoid that fate? Then let’s explore the common nightmares of leather welding jackets and reveal what every buyer should know before investing in their next set of welding gear.
1. Wondering About Leather Grade & Thickness?
Have you ever purchased a “heavy-duty” jacket, only to realize it feels suspiciously thin in certain areas? Do you know why inconsistencies in hide thickness can lead to weak spots that burn through or tear quickly? Could it be that some brands cut corners by using cheaper split leather, rather than more durable top-grain or full-grain hides?
Why does thickness matter so much in a welding jacket? Isn’t it because a consistent thickness across all panels means better heat resistance and longevity? And don’t welders deserve uniform protection for their chest, arms, and shoulders? When a manufacturer sources inconsistent hides, how can you be sure every inch of your jacket will withstand the same level of sparks and heat?
Quick Tip: Shouldn’t you ask suppliers directly about the type of leather they use (e.g., top-grain, full-grain, or split) and the minimum guaranteed thickness? Wouldn’t it be wise to look for product descriptions that detail hide quality, ensuring you’re not buying patchy or inconsistent material?
2. Concerned About Shoddy Tanning & Finishing Processes?
Do you hate strong chemical odors that worsen as your jacket heats up during work? Isn’t it unsettling to discover cracks or splits forming in the leather after just a few weeks of use? Could these problems stem from low-grade tanning processes that leave the leather dry, stiff, and prone to rapid deterioration?
What if you find the jacket is initially supple, but after a few hot shifts, it turns rigid and uncomfortable? Doesn’t poor tanning also lead to flaking or peeling of the outer layer, creating a safety risk when protective surfaces degrade?
Wouldn’t you rather invest in a jacket with high-quality tanning methods—ones that enhance flexibility and maintain softness over time? Why struggle with constant replacements and repairs when a well-tanned leather jacket could last for years?
3. Struggling with Overheating and Poor Breathability?
Doesn’t leather sometimes feel like wearing a furnace? Don’t welders need protection from sparks without suffocating in their own sweat? Aren’t stiff, improperly ventilated jackets known to cause fatigue, distraction, and even potential safety hazards?
How does cheap leather make heat retention worse? Isn’t it because subpar leather lacks the natural pores and finishing that permit breathability? Do you find yourself pausing work to air out, losing precious time and productivity?
Wouldn’t you prefer a jacket designed with slight perforations or well-placed gussets for increased airflow? Isn’t it worth seeking out designs that balance robust protection with some level of ventilation, so you can weld safely without feeling trapped?
4. Frustrated by Rapid Wear and Premature Damage?
Have you witnessed the leather surface start to flake, peel, or scuff within mere weeks? Isn’t it disappointing when an expensive piece of protective gear barely survives a standard workload? Do you realize the impact that frequent replacements have on your bottom line—especially in a busy industrial setting with multiple welders?
Could it be that the manufacturer saved costs by opting for cheaper splits or by skipping reinforcement patches at high-wear zones like shoulders, elbows, and chest? Aren’t those same zones the most susceptible to sparks, heat, and friction damage?
Isn’t it crucial to scrutinize brand reviews, specifically from professional welders who’ve tested the jackets in similar conditions? Shouldn’t you demand details about reinforcements like double-stitching and additional leather patches in stress points?
5. Worried About Inconsistent Quality Control Across Batches?
Have you ever received a bulk order of jackets for your team, only to find that half of them feel drastically different from the rest? Doesn’t that inconsistency sow confusion, frustration, and extra work for whoever handles safety gear procurement?
Why does this happen with even “famous” brands? Could it be that they source hides from multiple tanneries, failing to maintain strict quality standards? Isn’t this a nightmare scenario for a safety manager trying to ensure uniform protection for all employees?
What if each batch has unpredictable thickness, odor, or stiffness levels? How can you trust that the jacket you liked last year will be the same one you receive this year? Shouldn’t a reputable brand strive for the same excellence in every production run?
6. Do Weak Seams and Low-Grade Stitching Keep You Up at Night?
Have you noticed seams unraveling in the underarm area, rendering your jacket practically useless? Aren’t strong, heat-resistant threads just as crucial as the leather itself? Isn’t the entire protective suit compromised the moment seams start splitting?
Wouldn’t it be more cost-effective and safer to choose jackets with high-grade Kevlar® or similarly heat-resistant stitching? Why gamble on standard cotton or synthetic threads that can melt or weaken under constant exposure to sparks?
Isn’t it prudent to check for reinforced or double-stitched areas—especially in spots that experience frequent movement and strain? Wouldn’t that extra attention to detail extend the life of your jacket and save you the headache of premature repairs?
7. Feeling the Sting of Price vs. Performance Gaps?
Have you ever felt betrayed by a high price tag that didn’t equate to better quality? Could you be paying for a logo rather than substance? Is it possible that marketing and brand reputation sometimes overshadow actual performance data?
Does it make sense to buy a moderately priced jacket that lasts twice as long, instead of a famous brand piece that costs more but fails just as quickly—or even sooner? Aren’t you concerned about the total cost of ownership? Don’t frequent replacements or repairs add up to a much bigger sum over time?
Why not compare user feedback, technical specs, and real-world reviews before finalizing your purchase? Shouldn’t you inquire about bulk discounts or warranties that cover manufacturing defects, so you don’t waste money on repetitive replacements?
8. Shouldn’t You Demand Transparency and Solid Guarantees?
How do you feel about brands that dodge your questions about certifications or refuse to supply detailed product test results? Doesn’t that raise a red flag regarding compliance with safety standards such as NFPA 2112 or EN ISO 11611?
Why settle for vague assurances when you can look for third-party test documentation verifying flame-resistant properties? Isn’t it only fair that a brand offering “premium” leather also provides evidence of consistent quality and compliance?
Could a transparent return or warranty policy help you feel more secure in your purchase decision? Isn’t it logical to prioritize brands that confidently back up their products with repair or replacement guarantees?
Ready for Action? Here’s How to Choose the Right Leather Welding Jacket
Are you craving a step-by-step checklist for finding a leather welding jacket that meets your performance expectations? Would it help to break down the evaluation process into simple criteria that can guide you toward a better buying decision?
-
Check Leather Type:
Do you see clear descriptions mentioning “top-grain” or “full-grain” leather? Do you want to avoid split leather unless you verify its thickness and overall quality? -
Inspect Consistency & Thickness:
Is the hide even across all panels? Do you notice thin areas when you hold it up to the light? -
Evaluate Tanning & Finishing:
Does the leather smell chemically pungent or feel excessively stiff? Does the supplier mention eco-friendly or well-regulated tanning processes? -
Examine Stitching & Reinforcements:
Do seams appear strong and double-stitched? Are stress points reinforced with patches of extra leather? -
Prioritize Breathability & Comfort:
Are there any details about perforations, lining materials, or design elements that minimize overheating? -
Research Real-World Reviews:
Do actual welders praise or condemn the jacket’s durability? Can you find independent forums or social media groups discussing the brand? -
Compare Price vs. Lifespan:
Are you weighing the upfront cost against how frequently you’ll replace the jacket? Wouldn’t a slightly more expensive jacket that endures two or three times longer be the smarter choice? -
Confirm Warranty & Returns:
Does the company offer clear protections if the leather arrives faulty or underperforms within a certain time frame?
Final Thoughts: Will You Let Leather Quality Nightmares Haunt Your Safety?
Isn’t it time to protect yourself against cheap, poorly processed leather jackets that fail when you need them most? Wouldn’t your productivity, comfort, and safety all benefit from a well-informed purchase decision? Can you imagine the relief of never again wondering if your jacket will last through your next welding job?
With so many questions swirling around leather quality, do you feel better equipped to spot the red flags? When you finally secure a top-grade leather welding jacket from a trustworthy brand, won’t you rest easier—knowing you have the reliable protection you deserve?
Don’t let nightmares become your reality. Start by asking the right questions, analyzing each component of the jacket, and verifying the authenticity of any claims a brand makes. Because when it comes to your safety and your finances, shouldn’t you demand nothing less than genuine, long-lasting protection?
Now, are you ready to make an informed choice? Why wait any longer to upgrade your welding gear? After all, doesn’t your safety and peace of mind merit a jacket that stands up to the rigors of your demanding work environment?
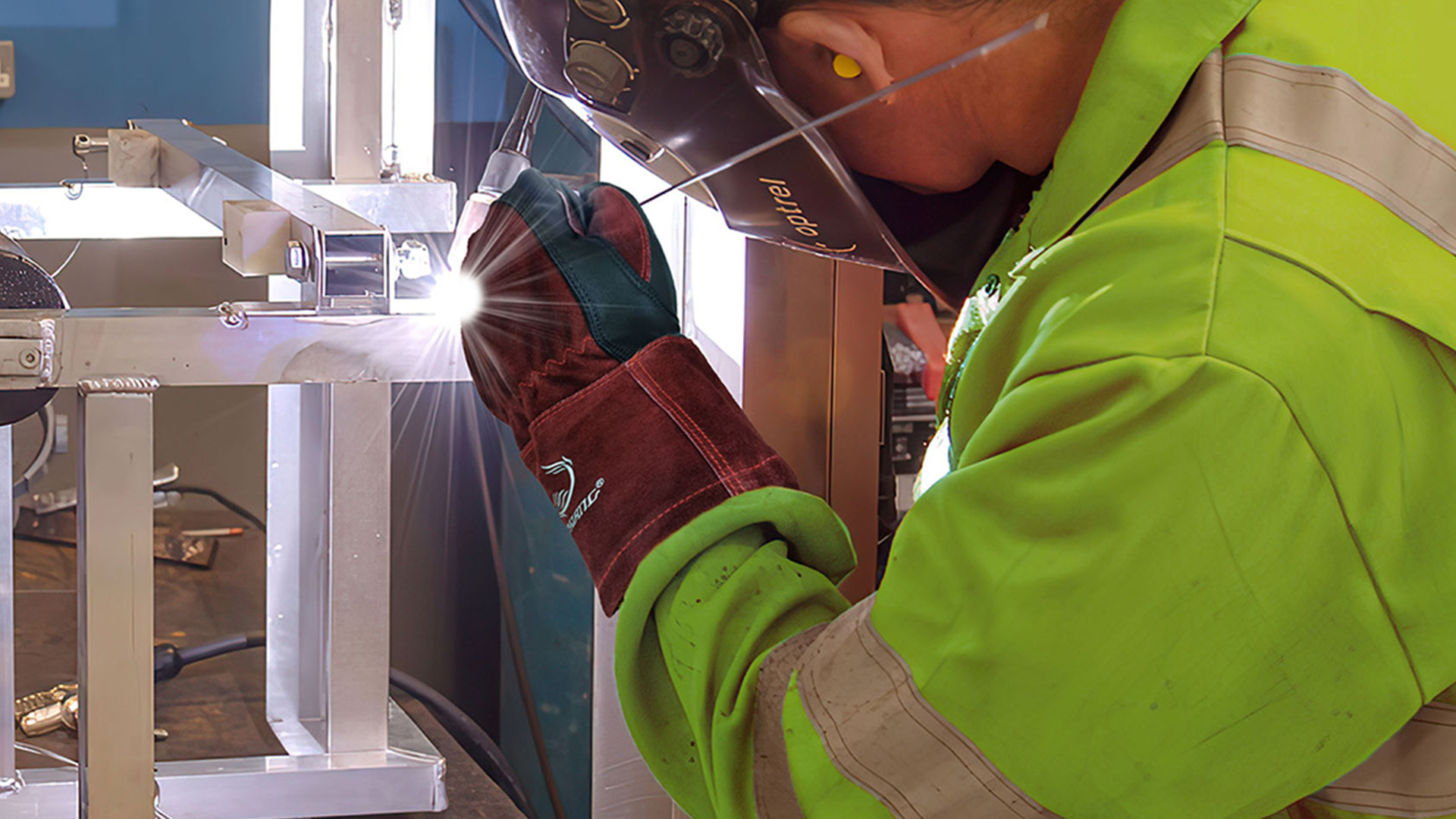