A close-up photograph of a welder using sturdy leather work gloves while operating welding equipment.
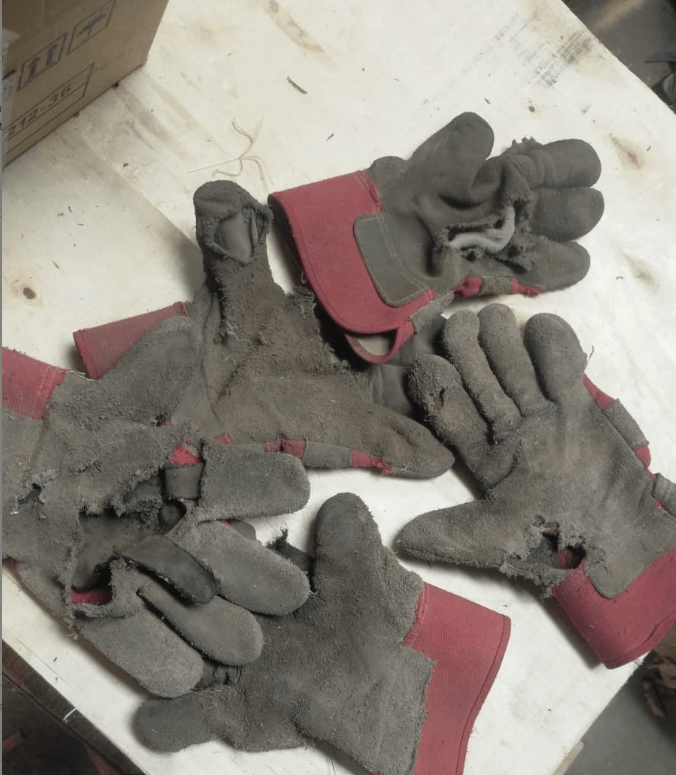
Have you ever purchased a pair of leather work gloves only to find that they didn’t last as long as you had hoped? Perhaps you noticed wear and tear, seams coming apart, or thinning material after just a few days of intensive use. This might spark questions: “Was there a manufacturing defect?” or “Did I pick the wrong gloves for my job?” or even “Is there a mismatch in expectations between buyer and seller?”
As the sales manager of a top manufacturer of welding safety products, I’ve encountered these questions countless times—especially from both professional welders and enthusiastic DIY hobbyists. Often, complaints center around the idea that their pair of gloves “only lasted 3–5 days.” This blog will tackle such concerns head-on. We’ll explore what real durability in leather work gloves means, how different work environments and intensity levels affect glove lifespan, and why one single factor (like the number of days you’ve used them) shouldn’t be the sole measure of quality. We’ll also discuss the importance of proper glove selection, correct storage and usage, and our commitment to quality assurance through returns and exchanges when there is a genuine defect.
By the end of this post, you will have a clearer, more holistic view of how to evaluate the durability of your leather work gloves, especially if you’re using them for welding safety or other heavy-duty tasks. We welcome your questions, provide guaranteed solutions for actual defects, and aim to help you match the right glove to your individual needs.
Why Focus on Leather Gloves for Welding Safety?
Q: Why do welders and other industrial workers often choose leather gloves?
A: Leather is a classic material with proven protective properties. From centuries past to modern industries today, leather has remained a favored choice. Here’s why:
- Heat Resistance: Leather is naturally resistant to heat, making it a prime choice for welders who are exposed to high temperatures and frequent sparks.
- Durability Under Stress: Well-chosen leather offers robust wear resistance, protecting your hands against rough surfaces, abrasions, and mechanical stress.
- Comfort & Flexibility: Leather molds to your hands over time, providing comfort and dexterity, essential elements for tasks like welding where precision is key.
- Protection from Spatter: Leather does not easily catch fire or melt, offering a crucial safety advantage for heavy-duty work involving sparks, spatter, or molten metal.
It’s this unique combination of qualities—heat resistance, mechanical strength, and comfort—that makes leather gloves so popular in welding safety contexts. However, their performance relies on several factors: the quality of the leather, glove design, the specific environment in which they’re used, and the stress they experience on a daily basis.
The Durability Dilemma: “It Only Lasted 3–5 Days!”
Q: Does a glove failing after three to five days automatically mean it’s low-quality?
A: Not necessarily. While premature wear can certainly indicate a manufacturing defect, it can also be a sign of other issues—most notably, an intense usage scenario not matched to the glove’s intended purpose. Let’s break down some common culprits:
- Type of Leather: There are multiple grades and types of leather, ranging from cowhide and pigskin to goat leather. Each type has its own properties. Some are more flexible, some are more heat-resistant, and others are more abrasion-resistant. If you select a glove that isn’t suited for your particular welding or mechanical task, it might wear out quickly.
- Usage Environment: Are you working in extreme heat? Are you handling sharp metal edges or rebar all day long? High-friction environments accelerate wear on gloves. Even the best glove may see a drastically reduced lifespan in especially harsh conditions.
- Frequency of Use: Someone welding an hour a week for occasional DIY projects will likely get more lifespan out of the same gloves compared to a professional welder working 10-hour shifts daily. One user might say they’ve used the gloves for “three days,” but each of those days could mean 10 hours of rigorous, high-heat welding. Another user might casually use the gloves over a similar span of days but for far fewer hours in total.
- Maintenance and Storage: It’s easy to overlook how storing gloves in moist, dirty, or extremely hot spaces degrades the leather. Exposure to chemicals, oils, or direct heat sources can accelerate wear. Proper cleaning and drying routines can significantly extend the glove’s performance over time.
When Manufacturing Defects Do Occur—Our Quality Assurance
Let’s be clear: If there is a genuine manufacturing defect, you should not have to tolerate subpar gloves. Our brand is built on the promise of top-tier welding safety equipment. If a seam unravels prematurely, if the stitching is inconsistent, or if the material shows clear signs of flawed workmanship, we take responsibility.
Q: What if I strongly believe my gloves have a factory defect?
A: We encourage you to reach out immediately. We offer a straightforward return or exchange policy for cases of confirmed manufacturing defects. Once we inspect your returned gloves, we’ll identify if the issue is indeed a flaw in materials or production. We are committed to delivering the quality you deserve.
Remember, our goal isn’t to dodge accountability but to ensure that you have the right product for your needs. Returns and exchanges help us collect feedback, improve our processes, and maintain the high standards our customers expect.
Comparing Buyer vs. Seller Perspectives on Durability
Q: Why does it sometimes feel like there’s a big gap between a seller’s promise of durability and a buyer’s real-world experience?
A: Durability is a multi-faceted concept. From a manufacturer’s viewpoint, “durable” means that under normal, recommended conditions, a product maintains its protective properties for a reasonable period. From a buyer’s perspective, that “reasonable period” can vary drastically based on:
- Personal Workload: One user might put 40 hours of intense labor into a glove every week, whereas another user might only work 2–3 hours occasionally.
- Job Hazards: If your daily tasks involve handling extremely abrasive metals, or if you’re frequently dealing with sharp edges, your gloves will obviously degrade faster than if you only manage mild to moderate tasks.
- Expectations & Previous Experiences: If you’ve used the same glove brand or style for years and they typically lasted two months, you’d understandably be upset if a new pair wore out after a couple of weeks. Sometimes, though, raw material changes or product design modifications might alter the expected lifespan, leading to confusion.
The biggest takeaway is that no single factor—like “they lasted three days”—can completely define whether gloves are truly durable or not. That said, we fully acknowledge how frustrating it can be to invest in new leather work gloves only to see them wear out rapidly. Therefore, we encourage communication: let us know your specific working conditions and expectations so we can better help you pick a glove model that meets or exceeds your needs.
Choosing the Right Leather Work Gloves for Your Task
Q: How do I know if I’ve selected the right gloves for welding safety or other industrial tasks?
A: Here are some crucial considerations:
- Leather Type:
- Cowhide: Popular for its robust nature, good heat resistance, and decent comfort. A great general-purpose choice for welders.
- Goatskin: Known for its dexterity, making it ideal for tasks requiring finer hand movements. However, it may not be as heat-resistant as heavier hides.
- Pigskin: Usually has excellent breathability and flexibility, but might not resist heat as effectively as cowhide.
- Split vs. Grain Leather: Split leather is taken from the underside, offering rugged protection but sometimes less dexterity. Grain leather comes from the outer side of the hide and generally features a smoother finish, greater dexterity, but potentially lower abrasion resistance compared to splits.
- Design & Construction: Look at how the gloves are stitched, whether they have reinforced palm areas, and if there’s adequate coverage around the cuffs. Features like wing thumbs or straight thumbs can also influence comfort and flexibility.
- Thermal Lining: Welders often need an inner layer that provides additional insulation from heat. If you’re performing high-heat tasks, look for gloves specifically marketed with heat-resistant linings or Kevlar stitching.
- Size and Fit: Gloves that are too tight can restrict blood flow and dexterity. Too loose, and they might slip off or compromise safety. Make sure you measure your hand accurately and refer to the manufacturer’s sizing chart.
- Certifications and Ratings: Check whether the gloves meet relevant standards (like EN 388 for mechanical risks in some regions, or EN 407 for thermal risks, or ASTM standards in the U.S.). These ratings give you a quantifiable sense of the glove’s protective capabilities.
The Critical Role of Maintenance
Have you ever considered that proper maintenance can nearly double the lifespan of leather work gloves? It’s a game-changer. Here’s how to care for them:
- Regular Cleaning: Wipe off metal dust, debris, or chemicals after each use. If you’re dealing with grease or oil, use appropriate cleaning solutions recommended by your glove’s manufacturer. Avoid drenching the gloves in water, as excessive moisture can cause leather to stiffen or crack when dried.
- Proper Drying: When your gloves get wet (from water or sweat), allow them to air-dry at room temperature. Do not place them in direct sunlight, on a radiator, or use a blow dryer—extreme heat can shrink or damage the leather.
- Condition the Leather: If recommended by the manufacturer, apply a suitable leather conditioner to keep the material supple and crack-free. This helps maintain both comfort and protective capabilities.
- Storage: Store your gloves in a cool, dry place away from direct heat sources or exposure to chemicals. Dirty, humid workshops can hasten deterioration.
By following these steps, you’re not only preserving the materials but also ensuring that the gloves continue to provide maximum safety. Remember, maintenance is part of the usage process—neglecting it can cause even the highest quality glove to fail prematurely.
Our Commitment: Quality, Communication, and Clarity
Q: What if I still feel uncertain whether my usage scenario is too harsh for a particular glove model?
A: Reach out to us. We believe in transparent communication. We can recommend which glove lines stand up better under intense friction, high heat, or prolonged daily wear. If you’re experiencing repeated glove failures, it might be that you need to switch to a heavier-duty product line or incorporate more frequent replacement intervals based on your specific job.
Q: What if I simply have unrealistic expectations about how long a pair of gloves can last?
A: That’s where clarity is key. Let’s discuss the typical lifespan for gloves in an environment similar to yours. If you are using them in extremely abrasive conditions, it may be necessary to rotate multiple pairs to avoid concentrated wear on a single pair. Understanding the realistic performance window helps you budget properly for your protective equipment and ensures consistent safety on the job.
Q: Are we just making excuses for lower-than-expected durability?
A: Absolutely not. We’re passionate about providing top-quality welding safety and leather work gloves for professionals and hobbyists alike. True, there can be occasional defects—no manufacturer is immune to that. But just as often, it’s a question of matching the right glove design and material to the specific challenge, combined with proper care and realistic expectations.
Conclusion
In the world of welding safety and industrial work, the notion of “durability” is much broader than just counting the days your gloves last. Properly chosen and well-maintained, a pair of leather work gloves can be a trusted ally for welders, mechanics, and countless other tradespeople. Yet if your gloves do fail in what you believe is an unreasonably short time, we encourage you to get in touch. We stand by our products with return and exchange policies specifically for manufacturing defects. At the same time, we urge you to look deeper into factors such as your work environment, usage intensity, and maintenance routines. Doing so helps us provide you with the most appropriate glove solution and fosters a clearer understanding of how to define “true durability.”
Ready to find the perfect gloves for your welding safety needs? We’re here to guide you. With years of experience and a commitment to continuous improvement, our team is on hand to answer any queries you may have. Don’t hesitate to reach out if you need personalized recommendations. Your safety, comfort, and satisfaction remain our top priorities.
If you’re still not sure which glove style to choose or have concerns about whether your specific environment is too demanding for a particular type of leather, ask us. Our experts can help you weigh your options, ensuring you’re equipped with gloves that offer optimal protection and a satisfactory lifespan. After all, safety gear is an investment—when you choose wisely and maintain your gloves properly, you’re investing in your own safety and productivity.
Thank you for reading, and remember: “It’s not just about how long a glove lasts—it’s about choosing the right glove, caring for it properly, and using it in the right way.” We look forward to partnering with you to keep your hands protected, your tasks on track, and your workdays productive.
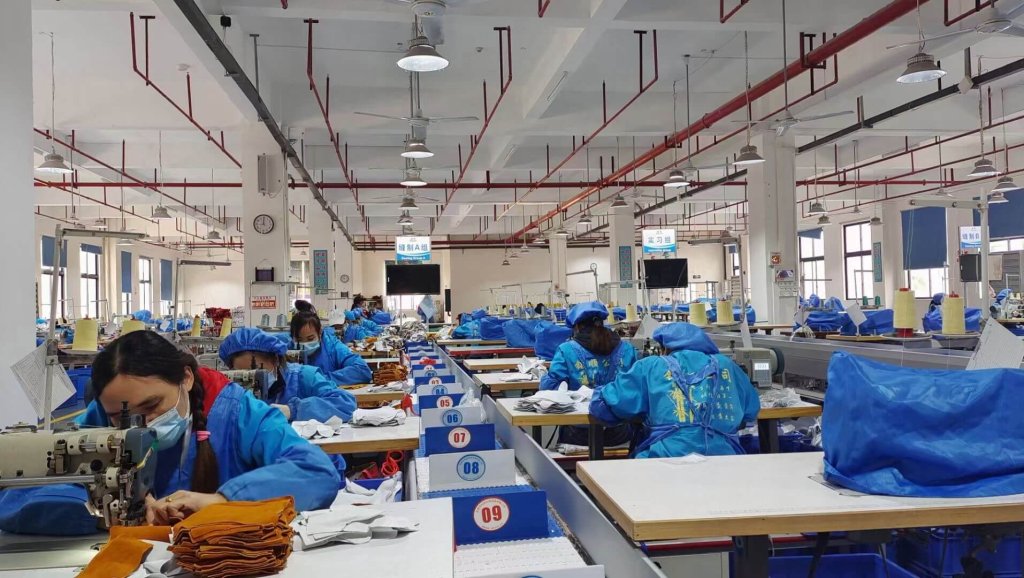