Finding a high-quality welding jacket is essential for anyone serious about welding safety. These jackets aren’t just about comfort; they’re critical for protecting against intense heat, sparks, and possible burns. Given the variety of jackets available, how do you pick the best one? Here, we’ll explore the key factors to consider when selecting a welding jacket, focusing on why jackets made by manufacturers with their own tannery and OEM expertise tend to offer top-quality, durability, and reliability.
Why Quality Matters in Welding Jackets
A welding jacket is more than just clothing; it’s essential protective equipment. High-quality jackets use superior materials to withstand harsh environments, and they last longer while delivering better performance. This can enhance comfort, productivity, and safety, making a significant difference in demanding welding settings.
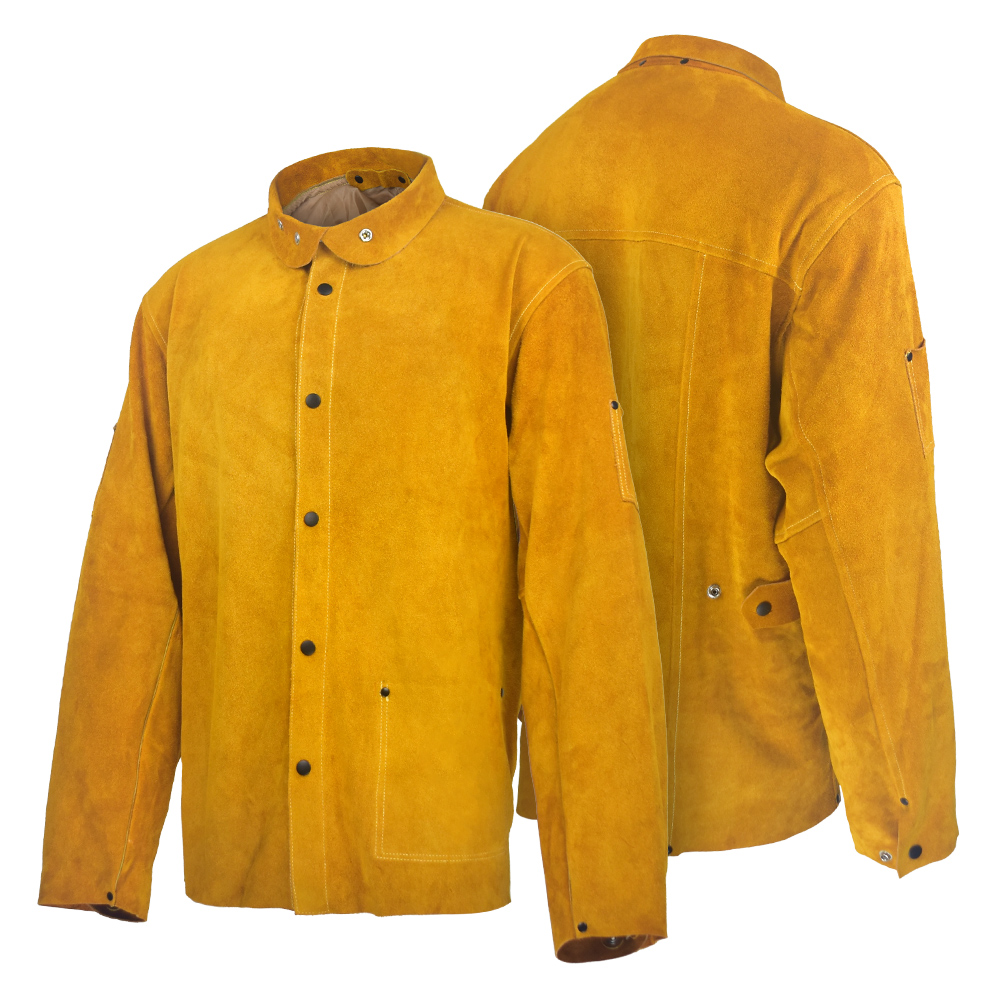
1. Choose the Right Material
Welding jackets come in a few different materials, each suited for specific tasks and protection levels:
Leather: Known for its durability and heat resistance, leather is the most common material for heavy-duty welding. Jackets made from top-grain or split leather provide high-level protection. When a factory owns its tannery, it can manage the leather quality directly, optimizing heat resistance and flexibility to produce jackets that deliver both comfort and superior safety.
FR Cotton: Flame-resistant cotton jackets are popular for lighter welding tasks. They’re treated with flame-retardant chemicals to meet safety standards, though they don’t provide the same heat protection as leather, making them better suited for low-intensity work.
Combination Materials: Some jackets use a blend, with leather in high-risk areas (like the shoulders and sleeves) and lighter, breathable materials elsewhere. This gives a balanced mix of protection and comfort.
2. Check for Heat and Flame Resistance
Quality welding jackets should meet industry safety standards, like NFPA 2112 for flame-resistant clothing. Choose jackets that provide reinforced protection in critical areas. Manufacturers with OEM expertise typically follow strict testing standards, ensuring each jacket withstands intense conditions and offers optimal protection.
3. Consider Weight and Flexibility
Weight and flexibility are essential factors. Jackets that are overly heavy or stiff can limit movement and cause fatigue, so finding a balance between protection and mobility is crucial. Some manufacturers treat leather to make it more flexible and comfortable, especially when they control leather processing in their own tannery.
4. Look for Comfort Features
Comfort is not a luxury; it’s a necessity in welding. Here are some comfort features to look for:
· Ventilation: Underarm vents or mesh panels help reduce sweating and keep you comfortable during long hours of work.
· Adjustable Cuffs and Waist: These prevent sparks from entering the jacket and ensure a snug fit.
· Lining: A quality lining can wick away moisture and make the jacket more comfortable against your skin.
5. Evaluate Durability and Stitching
A high-quality welding jacket will have reinforced stitching that withstands heavy-duty use. Double-stitched or reinforced seams prevent fraying and ensure that the jacket stays intact under extreme conditions. In premium models, Kevlar thread is often used to add extra durability, especially from experienced OEM manufacturers.
6. Select the Right Size
Getting the right size is crucial for protection and mobility. A properly fitted welding jacket should allow enough room for movement without being too loose or tight. Loose jackets can catch on equipment, while tight jackets can restrict movement. Many OEM manufacturers offer a range of sizes, and some may even provide customized sizing options for a more precise fit.
7. Choose Reliable Brands and OEM Manufacturers
Choosing a jacket from an OEM manufacturer with a strong track record is a smart choice. OEM manufacturers typically produce jackets for well-known brands, adhering to high-quality standards across their products. When the manufacturer owns a tannery, they have even more control over material quality, ensuring a consistently high level of heat resistance, durability, and comfort.
Mingshun owns a split tannery for a stable welding jackets’ raw materials.We know what’s best quality of welding jackets,we know why other manufacturers faces problems like leather goes mold,gets harden.We know how to tannery leather and that’s why we can guanratee customers with quality with return policy.
Investing in a quality welding jacket means investing in safety, comfort, and long-term performance. By choosing a jacket from a reputable manufacturer with OEM expertise and in-house leather processing, you ensure that your protective gear meets the highest standards. Look for one that fits well, meets safety certifications, and has comfort features to stay protected and productive, no matter the job.
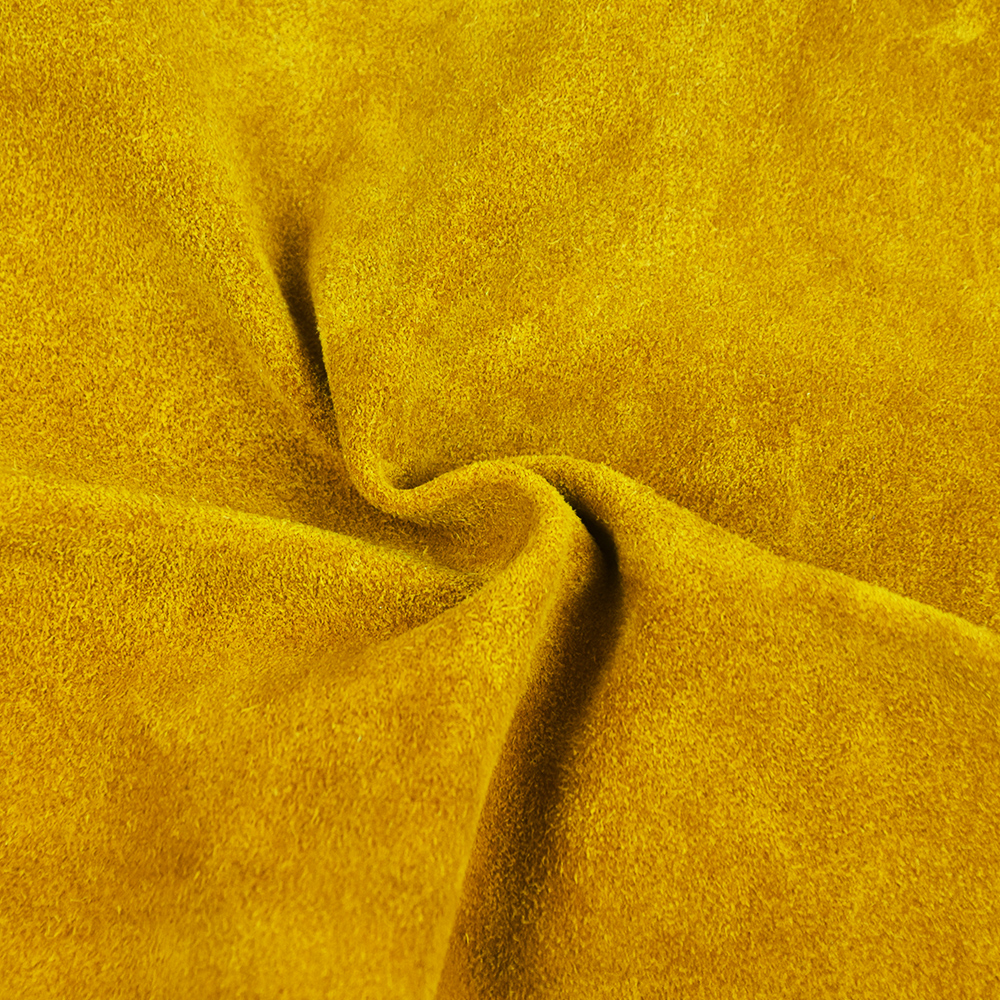